Customer care
Our Customer Care division guarantees your peace of mind, wherever your plant is located.
The partnership with our customers doesn’t end after commissioning. We provide after-sales support to guarantee the production continuity of your installation.
We take care of separate orders, spare parts, inspection, maintenance, training, process and concept engineering, technical support and repairs, with customer-oriented technical support. Send your questions by mail to service@j-tec.com.
Enhancing Spare Parts Profitability and Revenue Through Logistics Maturity Levels
Enhancing Spare Parts Profitability and Revenue Through Logistics Maturity Levels
In the fast-paced world of Original Equipment Manufacturers (OEMs), the efficiency and effectiveness of spare parts logistics operations are crucial for profitability and revenue: “Spare Parts are the cash cow of the company”. Advancing through different levels of logistics maturity, being: Basic, Intermediate, Mature, and Advanced, can significantly enhance spare parts profitability and revenue by leveraging improvements in Inventory Management, Distribution Network Efficiency, Technology, Sustainability, and Customer Satisfaction. This article explores how the logistics maturity level impacts profitability and revenue.
Each level represents a step change in the sophistication and efficiency of logistics operations, influencing various key factors that drive profitability and revenue.
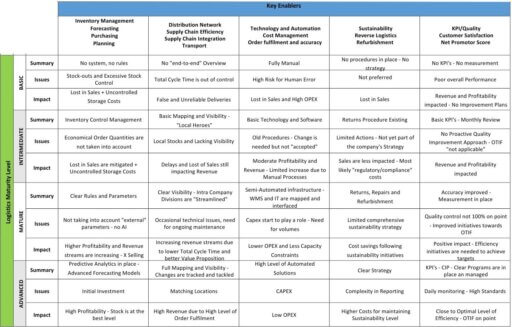
Source : Katoen Natie – Division Aftermarket – 06/2024
Katoen Natie’s Role in Enhancing Spare Parts Logistics Maturity
Katoen Natie, a global leader in logistics services, plays a crucial role in supporting its partners to advance through these maturity levels, thereby enhancing their spare parts profitability and revenue. By forming long-term partnerships and focusing on continuous improvement, Katoen Natie provides comprehensive support at each stage of logistics maturity.
Customized Solutions and Technology Integration
Katoen Natie offers tailored solutions to meet the specific needs of each partner. This includes implementing basic ERP systems at the Intermediate level to integrating advanced technologies at the Advanced level. These solutions ensure that partners have access to the latest tools and systems required for efficient logistics operations.
Enhancing Visibility and Flexibility
Through state-of-the-art technology and data analytics, Katoen Natie provides real-time visibility into inventory and supply chain operations. This transparency enables partners to respond quickly to market changes, increasing operational flexibility and reducing the risk of stockouts or excess inventory.
Supply Chain Integration and Collaboration
Katoen Natie fosters robust supply chain integration, facilitating seamless coordination between suppliers, manufacturers, and other stakeholders. This integration ensures smooth operations and efficient logistics processes, contributing to overall profitability and customer satisfaction.
Optimizing Labor Management and Reducing Operational Costs
By leveraging automation and advanced workforce management systems, Katoen Natie helps partners by optimizing labour management. This optimization reduces operational costs while maintaining high service levels, crucial for improving profitability at all maturity stages.
Boosting Customer Satisfaction
Katoen Natie’s commitment to excellence ensures that partners can meet and exceed customer expectations. Reliable and timely delivery of spare parts, coupled with exceptional service quality, leads to higher customer satisfaction and loyalty, which is essential for long-term profitability and increasing revenue.
Conclusion
The maturity level of spare parts logistics operations plays a critical role in determining spare parts profitability and revenue. Advancing from Basic to Intermediate, Mature, and finally to the Advanced level unlocks significant improvements in key factors such as technology utilization, visibility, flexibility, supply chain integration, labour management, operational costs, and customer satisfaction. Each of these factors contributes to a more efficient, cost-effective, and customer-centric spare parts logistics operation.
Katoen Natie’s expertise and support in logistics services empower its partners to navigate through these maturity levels effectively. By fostering long-term partnerships and focusing on continuous improvement, Katoen Natie ensures its partners achieve optimal logistics performance and enhanced spare parts profitability and revenue, driving long-term success and customer satisfaction. By focusing on continuous improvement and leveraging advanced logistics capabilities, OEMs can significantly boost their spare parts profitability and revenue, ensuring long-term success and customer satisfaction.
For further insights and updates on the evolving landscape of Aftermarket, let’s stay connected.
Thibaut Van den Berghe
Market insights: Impact of Electrification on Aftermarket Business and Spare Parts Demand
The evolution of electrification within the automotive industry is set to significantly reshape the aftermarket business landscape and alter the dynamics of spare parts demand. The shift is marked by increasing production and sales of electric vehicles (EVs) globally, driven by environmental concerns, regulatory pressures, and advancements in battery technology. As a result, both OEMs and aftermarket players must adapt to this changing automotive landscape. This article outlines four key areas impacted by this trend:
- Rising Electrification Trends:
The automotive industry is witnessing a clear trend towards electrification, which significantly impacts the demand for spare parts in the automotive aftermarket business. The increase in EV production and sales highlights this momentum, prompting a need for aftermarket businesses to re-evaluate their strategies.

Source: International Energy Agency
- Impact on Aftermarket Business:
Electrification presents both challenges and opportunities for aftermarket businesses. Traditional internal combustion engine (ICE) vehicles have a broader range of spare parts, including many wear-and-tear components. In contrast, EVs have a simpler architecture with fewer moving parts and limited mechanical components. Consequently, demand for traditional spare parts, like engine components and exhaust systems, is anticipated to decline, potentially leading to revenue shortfall for aftermarket suppliers focused solely on ICE vehicles. However, market research indicates that the product life cycle of ICE vehicles is extending – up to 13 years compared to the previous 10 – providing a prolonged demand period for wear-and-tear parts.
Conversely, the rise of EVs opens new avenues for aftermarket businesses. The demand and availability of main components specific to electric powertrains, such as batteries, electric motors, and charging infrastructure, will increase steadily. This shift necessitates that aftermarket players diversify their product offerings and develop expertise in servicing and maintaining electric vehicles. The logistics of handling, storing, and distributing high-value components like batteries will be a challenge for logistics service providers supporting OEMs’ aftermarket business.
- Evolution of Spare Parts Demand and demand frequency:
The electrification of vehicles is expected to reshape the landscape of spare parts demand. While certain components will witness a decline in demand, there will be a surge in the requirement for electric-specific parts and accessories. Additionally, the longevity and durability of EV components may impact the frequency of replacements, potentially altering the aftermarket’s traditional revenue streams and business models.
Moreover, the introduction of new technologies, such as autonomous driving features and advanced driver-assistance systems (ADAS) in both EVs and ICE vehicles, will further influence demand for chassis and body parts. Aftermarket suppliers will need to adapt to the changing needs of modern vehicles to stay relevant.
- Strategic Imperatives for Aftermarket Players:
To thrive in this evolving landscape, aftermarket businesses must embrace innovation and invest in their R&D endeavours to develop specialized capabilities in servicing electric vehicles. Diversifying product portfolios to include both traditional and electric-specific spare parts will be vital to meet the evolving needs of customers and capitalize on emerging market opportunities.
Collaboration and partnerships with OEMs, technology providers, and other industry stakeholders will be vital for aftermarket players to stay abreast of technological advancements and market developments.
In summary, our aftermarket insights highlight the transformative impact of electrification on the aftermarket business and spare parts demand. While this transition presents challenges, it also offers lucrative opportunities for aftermarket players willing to adapt, innovate, and strategically position themselves to capitalize on the evolving automotive landscape.
For further insights and updates on the evolving landscape of Aftermarket, let’s stay connected.
Thibaut Van den Berghe
Navigating Warehouse Automation – Box Closing Solutions
Handling high parcel packing volumes through conventional, manual processes can be both costly and challenging. It often necessitates a wide range of box types, a high number of packing stations, and consequently, a large workforce and significant warehouse space to manage packaging activities and store various consumables.
To address such challenges, Katoen Natie frequently implements box closing automation solutions.
Choosing the Right Solution
The market is full of various box closing solutions with varying capabilities and limitations, and the cost of these solutions can also be substantial. Therefore, making the right choice is crucial, not only to establish a favorable business case, but also to ensure that the chosen solution both fits the needs of today as well as has the capability to be expanded for or adapted to the needs of tomorrow.
To identify the most suitable solution for our partners, we, at Katoen Natie, conduct a comprehensive analysis of the pertinent operational data and consider all the relating operational processes in order to identify the potential automation solution’s requirements and key design parameters, such as:
- Required throughput capacity
- Ideal box types and sizes
- Return-reusability
- Choice between glue (hot melt, etc.) or tape (paper, plastic, etc.)
- Reusability of inbound boxes from suppliers
- Other packaging requirements such as sustainability, labeling, document inclusion, and value-added service (VAS) activities. In partnership with Twintag, we have solutions that range from digital packing lists to paperless trucks. See the demo here: Twintag App
Understanding the Potential Benefits
In addition to increasing throughput, improving quality, and potentially reducing labor and storage costs, implementing a box closing automation solution, particularly one with box height reduction capability, can offer another major benefit: Less air in the boxes shipped.
This translates to:
- Reduced need for void filling, only protective materials required
- Enhanced stability and robustness of boxes
- Increased number of boxes stacked per pallet, resulting in potential savings on transportation costs
-
Looking for a 3PL partner?
Curious explore how our warehousing services can enhance your supply chain network?
Get in touch with one of our experts today and delve into how our warehousing services can add significant value to your operations.
Katoen Natie: A Preferred Partner and Expert in Industrial and Automotive Returnable Packaging Handling
Katoen Natie stands as a global leader in providing specialized services for Industrial and Automotive Packaging Handling Centers, providing tailored solutions to meet the intricate logistics needs of the industrial and automotive sectors. With over three decades of experience operating in various countries, Katoen Natie has honed its expertise to deliver efficient, cost-effective, and value-added services.
Advanced Logistics Operations:
Katoen Natie specializes in managing complex logistic operations associated with Industrial and Automotive returnable packaging pools. From receiving to storage, distribution, and reverse logistics, our streamlined processes ensure seamless flow and optimization of the supply chain.
Value Added Services:
Our Packaging Handling Centers offer a wide range of value-added services, including repairing, sorting, repairing, bundling, washing, and assembling of returnable packaging such as bins, KLTs, pallets, pallet frames and lids. By meticulously maintaining the quality and functionality of packaging materials, we contribute significantly to enhancing overall operational efficiency for automotive production facilities.

Tailored Solutions:
Recognizing the diverse needs of OEM’s, Katoen Natie provides tailored solutions designed to meet specific requirements. Whether it involves optimizing inventory management, implementing innovative technologies, or enhancing sustainability practices, our solutions are customized to drive success for our partners.

Global Experience:
With a robust presence across multiple countries, Katoen Natie brings extensive global experience to every project. Our deep understanding of local regulations, cultural nuances, and market dynamics enables us to navigate complexities and deliver consistent excellence across borders.
Commitment to Excellence:
At Katoen Natie, excellence isn’t merely a goal; it’s the cornerstone of our commitment. We continuously strive to improve our processes, invest in cutting-edge technologies, and uphold the highest standards of quality and safety. Our unwavering dedication to customer satisfaction ensures that we not only meet, but exceed expectations, driving success for our clients.
In conclusion, Katoen Natie’s unparalleled expertise in Industrial and Automotive Packaging Handling Centers, makes us the preferred partner for industrial and automotive manufacturers seeking reliable management of their returnable packaging materials and flows.
Ready to discover how Katoen Natie can tailor solutions to meet your specific needs?
Let’s connect.
Enhance Your Aftermarket Strategy: The Logistics Advantage with Katoen Natie
In the world of aftermarket services, a product’s journey extends well beyond its initial purchase. In today’s competitive environment, fine-tuning your aftermarket strategy is essential for sustaining customer satisfaction, fostering revenue growth, and maintaining a competitive edge. At Katoen Natie, we recognize the diverse advantages that aftermarket services bring not just to end customers, but also to your business’s profitability. We acknowledge that the real gauge of success lies in the ongoing performance and durability of your customers’ investments. Let’s explore three reasons why aftermarket services matter and what Katoen Natie can do for you.
Why Aftermarket Services Matter
- Enhance Customer Experience by maximizing equipment performance. Proactive maintenance and efficient supply chain management extend the lifespan of your equipment, reducing downtime and minimizing costly repairs of replacements. By offering timely maintenance, repair, and spare parts availability, you can ensure uninterrupted service for your customers, leading to higher satisfaction levels and recurrent business.
- Drive Revenue Opportunities. Beyond traditional product sales, aftermarket services present lucrative revenue streams through value-added offerings like remanufacturing, repair, and customization. Companies can tap into these opportunities to expand their market reach, capture additional market share, and drive sustainable revenue growth.
- Strengthen Brand Reputation. Investing in aftermarket services demonstrates a commitment to quality, reliability, and customer support, enhancing your brands’ reputation and fostering trust and loyalty among stakeholders.
-
- Specialized packaging for non-standard items
-

Our Role as a 3PL
- Expertise & Tailored Solutions: With decades of experience in aftermarket logistics and a deep understanding of various industries, we offer tailored solutions to meet each business’s unique requirements.
- Global Reach & Seamless Support: Our extensive global network of facilities and partners ensures seamless support for your aftermarket needs, no matter where you operate, providing you with an interconnected ecosystem.
- Commitment to Excellence & Partnerships: We prioritize customer satisfaction and partnerships, continuously improving our operations to deliver exceptional services, reflected in our high Net Promoter Scores (NPS). Our people-centric approach and private ownership advantage further contribute to our ability to provide reliable solutions and maintain focus on sustainability and community engagement.
- The aftermarket industry represents more than just an extension of initial product sales—it’s a critical component for long-term business success. It fosters customer satisfaction, strengthens brand loyalty, and opens doors to sustainable growth. Katoen Natie, as a trusted logistics partner, facilitates this transformation through tailored solutions and strategic collaborations. We empower companies to optimize their aftermarket strategies, achieve their business goals, and gain a competitive edge in the market through our industry expertise, global reach, and commitment to excellence. Ready to elevate your aftermarket strategy? Partner with Katoen Natie today and experience the difference firsthand.
For further insights and updates on the evolving landscape of Aftermarket, let’s stay connected.
Thibaut Van den Berghe
thibaut.vandenberghe@katoennatie.com
Three Advantages of Katoen Natie’s Strategic Position in Pet Food Logistics
Border Inspection Post (BIP)
At Katoen Natie Ghent, we have a Border Inspection Post (BIP) for pet food within our warehouse facility. This serves several important purposes to ensure the safety, quality, and compliance of pet food products entering Europe.
- Food Safety and Quality Assurance: Pet food must meet specific safety and quality standards. A BIP allows for the inspection of pet food products to verify compliance with the country’s regulations and standards for ingredients, labeling, and production processes.
- Regulatory Compliance: Different countries have varying regulations regarding pet food importation. This includes verifying proper documentation, labeling, and ingredient specifications.
- Customs and Import Duties: Border Inspection Posts also play a role in enforcing customs and import duties on imported pet food. Katoen Natie can provide these services at our Ghent platform to facilitate a smoother supply chain flow.
Border Inspection Post: Mid inspection process ensuring compliance with all required regulations and standards
In summary, a Border Inspection Post for pet food is a critical component of a country’s regulatory framework, ensuring that imported pet food products meet established safety and quality standards while also addressing Customs compliance.
Inland Barges
Imported Pet Food must be transported from the Port of Antwerp to our Ghent Multi-Customer platform via Inland Barges. While inland barges offer various advantages, their applicability depends on factors such as the availability and condition of waterways and destination points. In regions with well-developed inland waterway systems, barges can play a crucial role in the supply chain management of goods. Some of the key advantages include:
- Cost-Effectiveness: Inland barge transportation is often more cost-effective than road or rail transport, especially for large and bulky cargo. Barges can carry a significant amount of cargo in a single trip, reducing the overall cost per ton-mile.
- Sustainability: Barges are more fuel-efficient than trucks and trains on a per-ton basis. The lower fuel consumption per unit of cargo makes inland barge transportation an environmentally friendlier option, contributing to reduced greenhouse gas emissions.
- Reduced Congestion: Barges operate on rivers and canals, providing a separate and often underutilized transportation corridor. This helps alleviate congestion on roads and railways, leading to smoother traffic flow in urban areas.
- High Capacity: Inland barges have a high cargo capacity, allowing them to transport large volumes of goods in a single journey. This makes them particularly suitable for containers, bulk commodities, and raw materials.

The Ghent Container Yard Depot
A container yard depot, also known as a container depot or container yard, provides essential services for the storage, maintenance, and handling of shipping containers. There are several advantages associated with the use of a container yard depot in the shipping and Supply Chain:
- Intermodal Connectivity: Container yards are typically strategically located near ports, rail terminals, and major highways. This facilitates seamless intermodal transportation.
- Transshipment Hub: Container yard depots often serve as transshipment hubs for intermodal transportation. This facilitates the smooth flow of cargo between ships, trucks, and trains.
- Reduced Congestion: By efficiently managing container movements, container yards contribute to reducing congestion at ports and terminals. This helps to streamline the overall supply chain.
In summary, container yard depots play a crucial role in optimizing the handling of shipping containers, contributing to the efficiency, security, and reliability of the global supply chain. Their strategic location and services support the smooth flow of goods.
In a world where efficiency, sustainability and accessibility for warehousing operations is important, Katoen Natie’s strategic multi-customer platform offers a seamless and cost efficient solution for Pet Food businesses looking to leverage the economic advantages of this thriving region.
For further insights and updates on the evolving landscape of Pet Food and Pet Care, let’s stay connected.
Bart Versprille
Katoen Natie announces major investments in the Netherlands
Chemelot
Covering an area of over 800 hectares, the Chemelot site is one of the major chemical hubs in Europe and has been expanding in recent years. The integrated cluster of companies produces a variety of chemicals and performance plastics for a wide range of markets and applications. Chemelot also hosts a research campus, with over 8,000 people working on-site.
Katoen Natie investments
Since 2013, Katoen Natie has acquired a number of logistics terminals in Limburg. Its sites in Nuth, Born, Geleen, Elsloo, Tüddern and Maasmechelen currently employ 250 people. With the expansion, Katoen Natie will anchor its strategic presence in the region.
Central to the investment is a 12 hectare green field project on the Chemelot site. Here, Katoen Natie will build a brand new multi-customer terminal consisting of 54,500 m² state-of-the-art warehouse and 207 silos. Aside from warehousing operations, Katoen Natie will offer a full range value-added services including repackaging of chemicals, purifying of contaminated products, compounding and compacting services. The Chemelot terminal is expected to be operational in Q2, 2020.
In addition to the investments on-site, Katoen Natie will expand its Nuth logistics terminal with 10,000 m² of warehouse space and 60 silos expected to be operational by the end of 2019. Another plot of land was acquired at Mitsubishi Avenue in Born, where Katoen Natie will construct and operate a 35,000m² warehouse to service the automotive industry.
Investments in the local transport capacity will continue over the next year. With the purchase of 115 new lorries, 45 dry bulk trailers and 10 liquid bulk trailers the existing fleet will be renewed and expanded.
Gateway to Central and Eastern Europe
Aside from their proximity to Chemelot, the Katoen Natie terminals in Limburg are located just a few kilometers from the Belgian and German border. This strategic location, close to the ports of Antwerp
and Rotterdam and with easy rail and water access, make them an ideal stepping-stone for import flows into the Ruhr area and Eastern Europe.
With this expansion, Katoen Natie affirms its position as the leading logistics and industrial services provider for the chemical industry in Europe. The implantation of its logistics platform on the Chemelot site will produce significant transport savings for Katoen Natie’s existing customers and reduce overall CO₂-emissions. In total, the 100,000 m² of added warehouse capacity and value-added logistics operations will create 75 new full time jobs in the region.
Katoen Natie
Katoen Natie is a private Flemish enterprise and its activities consist of value add logistical services with activities in 30 countries and more than 13.000 employees.
For more about Katoen Natie go to https://www.katoennatie.com/who-we-are/
Visitor’s privacy policy
During your visit to one of our premises we may process your personal data. This Visitor’s Privacy Policy is written to inform you of which personal data we will collect during your visit and how we use it. We will only process your personal data as described below and will never sell, license, rent, or make public your personal data.
Katoen Natie recognizes the importance of data protection and privacy of personal data and will handle all personal data of the data subject with appropriate care. Katoen Natie explicitly confirms that all personal data will be handled according to the Belgian law of December 8th, 1992 and according to the GDPR Regulation 2016/679 of April 27th, 2016 concerning the protection of natural persons in regard to the processing of personal data and free traffic of personal data (hereafter GDPR).
Data privacy is very important, please take the time to read this policy carefully.
Use of the personal data
Processing of your personal data based on the need to meet legal obligations and the Controller’s legitimate interest to ensure a safe and secure work environment, in some cases applicable law might require consent of the data subject, in those cases Katoen Natie will ask for explicit consent to process your personal data.
Your personal data is processed for reasons of security and safety on our premises. In addition to our terminal-rules which everyone needs to abide by, we need to know who is and/or has been on our premises for your own personal safety in case of an alarm and to ensure the security of our operations and our property as well as the property entrusted to us by our clients. This is done, amongst others methods, by way of using entry control such as visitor log’s, badging, as well as camera recordings (whether or not including sound).
The storage duration might vary: 1 month for camera recordings and 6 months for sign-in and badging records. Notwithstanding the foregoing, any personal data that may give rise to legal effects, can be archived for evidentiary purposes for a period equal to the statute of limitation (most often 10 years). All personal data which is no longer required for any of the above mentioned purposes or any other (legal) purpose will be anonymized and/or permanently removed.
Recipients and transfers
Your personal data may be transferred to servers located outside the country in which you live or to affiliated companies or any agents or consultants so that they may process personal data on our behalf. We will use best efforts to guarantee that these recipients shall process your personal data in compliance with the applicable legislation. Such recipients may be located outside the European Economic Area, such as Moldova and Macedonia. In the case of any such transfers, we use best efforts to ensure that your personal data is adequately safeguarded through the implementation of standard data protection clauses adopted by the Commission.
Information we will collect
We may request the following information: name, contact details such as professional phone number, address, the company you work for, e-mail address and your contact person within our company. On some occasions you will receive a badge to use for entering our premises. A log is kept for every use of such badge. In addition, from the moment you enter our premises until your leaving, you might enter zones with camera surveillance, which are indicated in accordance with the applicable laws.
In all forms you have to fill out the optional information will be marked with an asterisk (*). It is your choice to provide such marked information, but you are in no way obliged fill those out.
Managing your personal data (rights)
As data subject you have the following rights as they are defined by the applicable laws:
Subject to the conditions in the applicable law, you have the right to request:
- Access to your personal data;
- A copy of the personal data we hold about you in a commonly used format and transfer of your personal data to a third party of your choosing;
- Restriction of processing and/or the right to object to the processing of your personal data;
- Correction or update of your personal data;
- Erasure of all or part of your personal data;
- To the extent that any processing is based on your consent, you can withdraw it any time, without this affecting the lawfulness of past processing.
In addition, you can lodge a complaint and/or report any misuse of your personal data to the national data protection supervisory authority.
Please note that most of the personal data collected is required for the safety and security of our business and/or required by law. If you refuse to provide such information or ask to have such information deleted in accordance with this policy, it is impossible for us to grant you access to our premises.
Security
We protect your information as our own and have implemented several safety and security measures for our IT-network such as firewalling, use of access rights and multifactor authentication, advanced threat protection (by using threat intelligence feeds), patch and vulnerability management. In case your personal data is processed by third parties we use best efforts to ensure the same or similar protection measures.
Changes
This Privacy Policy will be subject to future changes in order to guarantee the best protection of your personal data. Small changes will be published on our intranet and website, significant changes will be communicated more extensively. We invite you to regularly check this policy and stay informed on how we use your personal data.
Contact information
If you have any questions or wish to exercises your rights please contact us via infosec@katoennatie.com .
To assist us in swiftly dealing with your request, please provide your full contact details in such request. We might demand further proof of identity to handle such a request.